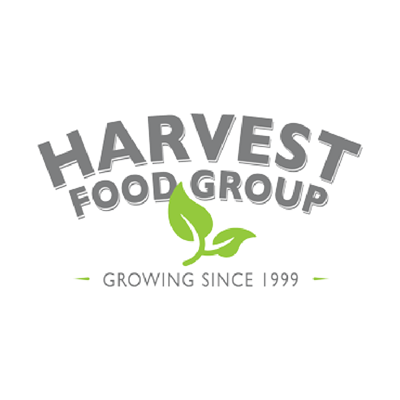
Harvest Food Group (HFG) is a family-owned business based in Naperville, Illinois. The company leads the food and beverage industry in individually-quick-frozen (IQF) foods, supplying quality fruits, vegetables, grains and more across the globe. With a manufacturing plant based in Chicago, Illinois, HFG also serves as a collaborative co-packing solution and produces private label products for grocers. Additionally, the company created a retail line called Path of Life, which specializes in high quality, frozen side dishes made with clean and simple ingredients.
- Manual and time-consuming invoice process
- Lack of visibility and data accuracy
- Gaps in historical information and data integrity
- Improvement in accuracy of cycle counts from 6% to 98%
- Decrease in accounts receivable aging decreased from 5% to 1.6%
- Manual inventory checks eliminated
Overcoming Obstacles in Production
In 1999, Harvest Food Group (HFG) was founded by father and son duo, Philip and Jason Eckert, with only two telephones and a dial-up modem. Since then, HFG has evolved into a leading manufacturer in the food and beverage industry as it strives to create products with clean and thoughtfully sourced ingredients from growers across the world. The HFG portfolio grew to encompass family-owned startups to international suppliers and everything in between, and recognized a gap in its existing, paper-based system. While this framework tracked items produced and the business finances, it was otherwise limited.
Challenge
Urgent Need for New ERP
One major issue became clear: HFG’s old system required manual confirmation of invoices on the final day of each month. As a result, the team needed to run all reports the night before a new month, forcing HFG to halt production as they carried out this tedious process. In instances where production began too soon, reporting started over from the beginning. Additionally, employees in finance were required to stay at the facility until late to oversee invoice completion. This system was not only demanding for the team, but also a strain on business.
With so few records stored in their current system, recalls and instances that required historical information left employees scattered, physically searching through boxes of paper files. HFG also had zero plant floor visibility. While they could see when production lines were running, additional details were scarce. There were also significant gaps in data due to manually recorded downtime—this lack of visibility and digitization made Overall Equipment Effectiveness (OEE) a mere dream for the HFG team.
Solution
A Smooth Go-Live Across the Company
The company’s overall lack of accountability and data integrity coupled with a desire for a more advanced system that could grow as business evolved led HFG to implement Plex ERP and Plex MES. The original system could no longer meet the company’s growing needs, so the HFG team hoped Plex could both fill in the gaps and also drive business forward with additional improvements.
HFG worked alongside a Plex project manager to maintain progress. All employees were granted access to the Plex training environment, which gave them step-by-step implementation instructions. The team also utilized a Gantt chart that illustrated the 16-phase go-live process in detail, broken down both by department and module within Plex. These assets provided a comprehensive view of the expectations and guidelines needed for successful implementation.
Initially, HFG’s go-live date was pushed by five months to give the team time to become well-versed and comfortable in Plex before completing the process. Different team members became directly involved as each module was implemented, testing operations and ensuring data accuracy before moving on to the next step. This allowed for a thorough understanding of Plex through each phase of the implementation, solidifying the decision to go live later than planned. The company went live successfully with Plex in August of 2018. They even opted to turn off access to the old system upon completion of the implementation to confirm that all employees were fully on Plex.
Result
Collaborating for Long-Term Success
Since implementing Plex, HFG has seen significant improvements. The most pressing issues were production shutdowns, which occurred once a month for manual invoices and an additional one week per year for full inventory counts. With Plex, HFG has not experienced any halts in production. Accounts Receivable (AR) aging has also decreased from 5% to 1.6%, an indicator that the company is now able to collect receivables more efficiently. HFG also now has historical data and real-time production information, allowing the team to be flexible and on top of any shortages or overages. Additionally, HFG has seen cycle count accuracy increase from 6% to 98%, which has drastically improved inventory management and helped to decrease manual labor.
Employees were hesitant to trust Plex at first, given the unreliable data provided by the previous system. However, over time, their distrust has been alleviated thanks to increased traceability and real-time data in Plex. The team can now see immediate results and have become better aligned with the shared goal of finding new solutions as HFG continues to improve scrap and OEE digitalization.
Jenny Crimmins, Senior Business Systems Analyst at HFG sums it up perfectly: “One of the nice things, which was a surprising result for me, was people’s motivation to want to continue to improve. Plex had a huge impact on the work done here and how it was done, and it opened people’s eyes to how fast things could be achieved.”
Looking ahead, HFG is excited for the future with Plex by their side. Currently, the team is in the process of implementing Plex Quality Management System (QMS), which will assist in the digitization of checklists and ultimately lead to expedited product handling at HFG. The company has exceeded their initial implementation goals and is committed to finding new ways to improve through Plex every day.
Published October 9, 2024