You may also be interested in
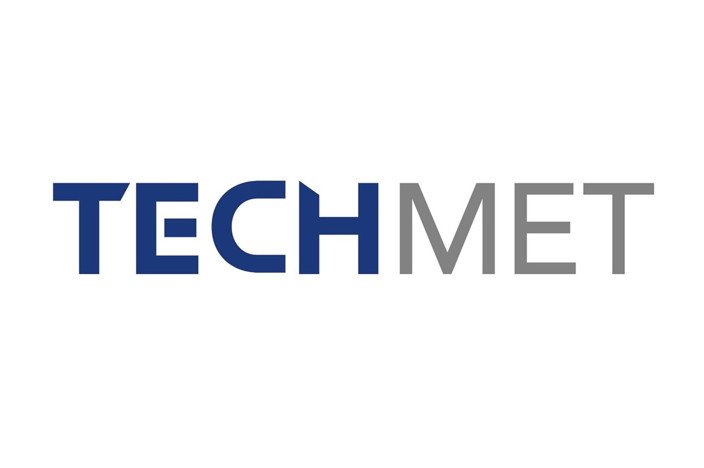
Tech Met Inc. is a leading provider of advanced chemical post-processing and surface treatments for the world’s most advanced additive manufacturing applications. Specializing in high performance metal alloys, Tech Met has served the aerospace, medical, industrial, and commercial markets with unprecedented precision and quality since 1988. From aircraft engine components to spinal implants, Tech Met's process control, lean practices, and six sigma certified project managers deliver quality assured products that meet the most rigorous specifications and are Nadcap AS7004 & AS7108 certified.
- Legacy, paper-based system provided no real-time, trustworthy data
- Lack of visibility into inventory and revenue data
- Slow invoicing process and less revenue realized
- Production and quality documents accessible from anywhere with cloud-based system
- Immediate invoicing and quicker revenue capture
- Companywide trust thanks to real-time visibility of inventory
Challenge
Off The Cloud and Paper-Based
Located just ten miles southwest of Pittsburgh, Pennsylvania-based Tech Met Inc. is a chemical milling company that primarily services medical and aerospace markets. As a service provider, Tech Met receives thousands of parts from customers, resurfaces the material to supplied prints, sends the products back out, and tracks each piece.
Their legacy system lacked the ability to provide real-time, trustworthy data. Reporting inaccuracies were common, making it difficult for plant managers to rely on the system to inform decision making. Production supervisors were frequently told materials were in stock when they weren’t, leading to delays, inefficiencies, and lost trust in the system across departments.
Tech Met expanded quickly over just a few years, growing from a handful of customers to adding larger-name clients onto their roster. The company knew that they needed a system in place to sustain their success. They had clear pain points that they needed their new system to address: lack of digitization, plant floor visibility, and real-time data. There was no single source of information for the company to operate from and most of their processes were tracked across various spreadsheets.
Additionally, as a contractor, Tech Met is required to keep production and quality documents for up to 30 years. This is a vast amount of documentation for any company to keep, especially when its primarily paper-based. Certain documents were stored off-site and could be difficult and time consuming to retrieve. With no digital ERP system in place, production visibility was provided by word of mouth. The company needed to transform and develop a reliable business system on which both employees and customers would be able to depend.
Solution
An Unexpected Implementation Journey
Tech Met put together a small taskforce to find the best ERP solution for the company’s needs. They reviewed many solutions. After a recommendation from their managed service provider, the company set their sights on the Plex ERP. It was Plex’s hands-on approach that set their software apart from the crowd. With the help of Rockwell Automation System Integrator (SI) Control+M Solutions, Tech Met participated in demos that showcased how Plex could fit within their existing infrastructure. After seeing the value that Plex could bring to the company, Tech Met moved forward.
The Plex implementation project kicked off in the beginning of 2020, dedicating a team to facilitate the process. Tech Met also worked alongside a project manager from Control+M Solutions, who they credit as playing a vital role in their implementation journey. The implementation took a sharp turn when faced with the COVID-19 pandemic and the implementation timeline was delayed.
In 2021, as the company started to emerge from the pandemic, Tech Met restarted the implementation process. The biggest task was figuring out how to transfer customer data from their current system into Plex. It became apparent that having individual process routers for each part was not feasible. Instead, Tech Met transferred their production steps in bulk. This decision sped up their implementation and generated positive project progress. There are currently over 2,000 parts in Plex and still more to go as Tech Met continues to integrate their processes. Although the implementation journey was longer than expected, Tech Met went live with Plex in October 2023.
Result
Streamlined Operations, More Revenue Realized, Companywide Trust
Tech Met has seen numerous benefits from migrating to Plex. Previously, Tech Met was largely paper-based and important documents were stored in multiple locations. Now, production and quality documents can be accessed in real time. With Plex’s cloud-based platform, these documents can be accessed anywhere. One of the biggest improvements has been the visibility Tech Met has gained into revenue and automating customer invoicing. Prior to Plex, production invoicing would take over a month to close out. Now, production closeout takes only a few days. Additionally, Tech Met can now bill customers instantly after a job has been shipped, which could take more than a week before implementing Plex.
Data is now both accurate and accessible. Before, inventory could sit and remain unassigned to a job. Now that employees have a better view of what products are in the facilities, they can more efficiently utilize on-hand inventory. This visibility has created a culture of trust within Tech Met, winning over even hesitant employees.
Looking ahead, there are plans to continue growing and optimizing their business. Tech Met hopes to implement Plex MES and QMS, continuing to automate processes and streamline quality data. The company is also working to fully integrate production planning into Plex. This integration would allow the company to benefit not only from production visibility but gain even more plant-floor visibility. With a successful year under their belt, Tech Met is excited about their future with Plex.
"Before Plex, we were siloed and unconnected. We were managing everything appropriately, but we were paper-based and doing lots of documentation rework. After Plex…there’s less paperwork, and we can realize revenue quicker. We have access to a vast amount of data and can catch errors much quicker than we had in the past."
Published June 12, 2025